

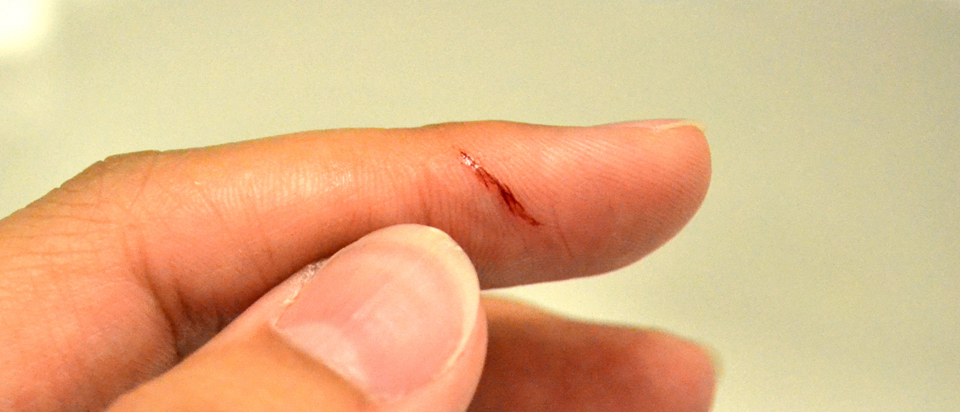
Here, you can see just how much degradation the old sensors had suffered over time. The next attempt (if any) to replace the sensors would have to be thoroughly thought through to prevent such damage. This was rather distressing as the work really took away from the look of the glove and would be difficult to repair. The glove's index and middle fingers were cut open in order to replace the sensors. In comparison, the new flex sensors were spot on. Much to my dissatisfaction, the original flex sensors proved to be useless as they gave inconsistent readings. Using a Pololu Arduino library for the IMU, motion data was easily captured by the Teensy, Gestures for the different finger positions had been designed previously, but for the time being, they would be eschewed in favor of simple open or closed states. A USB cable with its wires broken out supplied power from an available USB port. A 3.3V LDO was added to supply the power-hungry ESP, and voltage dividers were setup for testing the flex sensors. Having previously decided on the main components, a piece of protoboard was loaded up with headers for the microcontroller (a Teensy 3), a WiFi module (an ESP-01) and the IMU (an AltIMU-10 v4). The Power Glove electronics were removed, and the flex sensor wires were desoldered and lengthened for testing. What follows is a description of the work that went into the prototype, starting with. Still, the prototype was a success, and I felt I finally had enough content to bring the project here. Unfortunately, I found that I had started too late: I was able to get the drone in the air, but only AFTER the Faire was over. A co-worker suggested using the glove to fly a Parrot AR.Drone, and I set to work, re-purposing the existing boards using new electronics. The advent of the Las Vegas Mini Maker Faire spurred me to get the project up and running. I had been working on the project on and off up to that point, making plenty of conceptual prgress but only minor physical hacking. Sorry but I've seen too many prop strikes to ever want to see another.Before I finally get to the log detailing the new board design, allow me to take you on the quick detour that is the build log of the initial protoype. If the rpm had been lower - I doubt I would be typing this post so easily. The engine beng at medium rpm meant the prop was literally a disc and it 'knocked' my hand rather than letting it through. I have been 'nicked' by a 15" prop on front of a 15cc gasoline engine. Of course there are occasions like OP's that damage is limited. Sorry - but if anyone thinks that these props cannot do serious damage - then I hope you never have occasion to find out the truth of what they can really do. It took a large knife and grips to get that blade out. the blade sliced into the bench edge embedding itself half blade width into it. I have personal experience of an APC prop - again same material and similar size losing a blade during a bench test. Once that exited (came out on its own) - he regained the use of that finger about 90%. Turned out a sliver of GFN which is not picked up by X-Ray had lodged in the last joint area and prevented bending of the finger.

Paul lost the use of his index finger for months - Hospital could not find out why as they had stitched etc. Paul - a close friend of mine put his hand into a similar sized prop of same material - DJI props are made of GFN - that is Glass Reinforced Nylon. I suggest that your pal was extremely lucky.
